-
during sales
Tailored solutions for smart decisions: testing and advice during sales.
With our extensive expertise and knowledge, we provide comprehensive support throughout the sales process. Our team accompanies you every step of the way, offering valuable insights and guidance to ensure a successful outcome. Trust us to leverage our expertise for your benefit.
That's how Comexi helps you
Test our technologies in your real working environment.
Technical consulting to define the solution that fits your needs
Demo Center
0.2 Operational Maintenance
0.3 Print Unit Maintenance
0.4. Spare parts
Our system analyzes the demand for parts and makes a personalized offer of those elements most likely to render a machine inoperative. All this in order to minimize failure times and to be proactive in the delivery of consumables.
0.5 Cool (Comexi Ordering On Line)
A service open 24/7 and with a 5% discount!
0.2 Operational Maintenance
0.3 Print Unit Maintenance
0.4. Spare parts
Our system analyzes the demand for parts and makes a personalized offer of those elements most likely to render a machine inoperative. All this in order to minimize failure times and to be proactive in the delivery of consumables.
0.5 Cool (Comexi Ordering On Line)
A service open 24/7 and with a 5% discount!
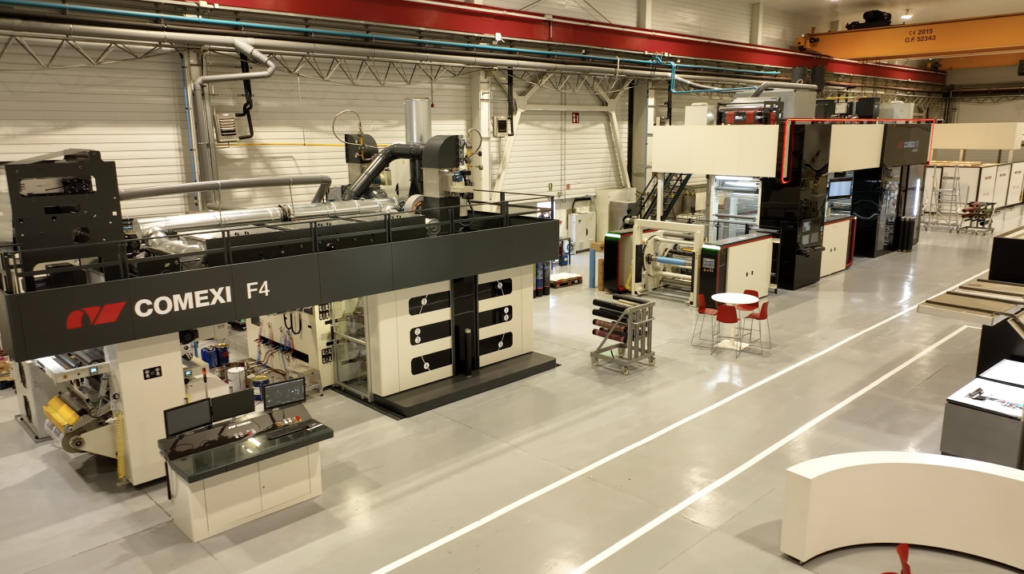
Technical consulting
0.2 Operational Maintenance
0.3 Print Unit Maintenance
0.4. Spare parts
Our system analyzes the demand for parts and makes a personalized offer of those elements most likely to render a machine inoperative. All this in order to minimize failure times and to be proactive in the delivery of consumables.
0.5 Cool (Comexi Ordering On Line)
A service open 24/7 and with a 5% discount!
0.2 Operational Maintenance
0.3 Print Unit Maintenance
0.4. Spare parts
Our system analyzes the demand for parts and makes a personalized offer of those elements most likely to render a machine inoperative. All this in order to minimize failure times and to be proactive in the delivery of consumables.
0.5 Cool (Comexi Ordering On Line)
A service open 24/7 and with a 5% discount!
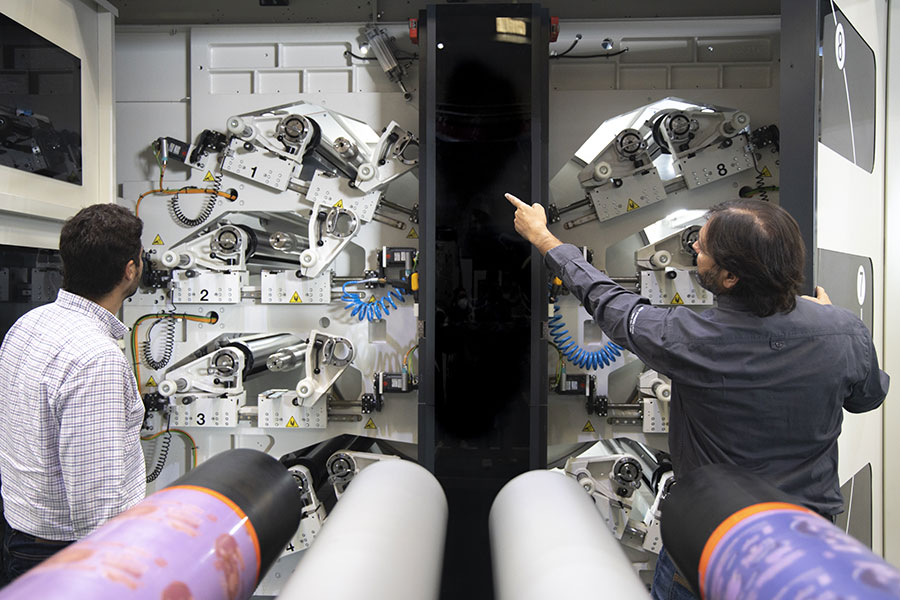