-
before sales
Expert guidance for high-quality. packaging: pre-sales consultancy.
The need to acquire new machinery for the conversion of flexible packaging is a complex and often long process. For this reason, at Comexi we accompany you from the beginning, helping you to define the main characteristics of your project.
That's how Comexi helps you:
Support and guidance to define your needs
Identify your production improvement points
Support
0.2 Operational Maintenance
0.3 Print Unit Maintenance
0.4. Spare parts
Our system analyzes the demand for parts and makes a personalized offer of those elements most likely to render a machine inoperative. All this in order to minimize failure times and to be proactive in the delivery of consumables.
0.5 Cool (Comexi Ordering On Line)
A service open 24/7 and with a 5% discount!
0.2 Operational Maintenance
0.3 Print Unit Maintenance
0.4. Spare parts
Our system analyzes the demand for parts and makes a personalized offer of those elements most likely to render a machine inoperative. All this in order to minimize failure times and to be proactive in the delivery of consumables.
0.5 Cool (Comexi Ordering On Line)
A service open 24/7 and with a 5% discount!
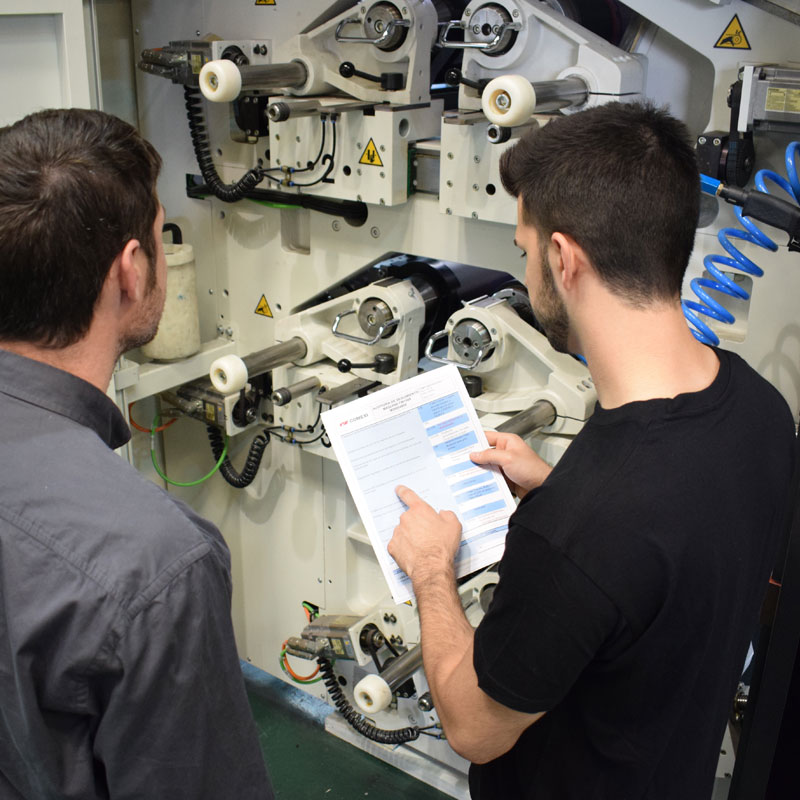
Consulting
0.2 Operational Maintenance
0.3 Print Unit Maintenance
0.4. Spare parts
Our system analyzes the demand for parts and makes a personalized offer of those elements most likely to render a machine inoperative. All this in order to minimize failure times and to be proactive in the delivery of consumables.
0.5 Cool (Comexi Ordering On Line)
A service open 24/7 and with a 5% discount!
0.2 Operational Maintenance
0.3 Print Unit Maintenance
0.4. Spare parts
Our system analyzes the demand for parts and makes a personalized offer of those elements most likely to render a machine inoperative. All this in order to minimize failure times and to be proactive in the delivery of consumables.
0.5 Cool (Comexi Ordering On Line)
A service open 24/7 and with a 5% discount!
